Hello! I am very interested in learning more about the potential of this product. Are there any Australian companies that would be able to give me more information on how to start a business in my area?
many thanks!
Blog Post
Greensulate – A fungus-based insulation material that's grown rather than manufactured

I had been reading about the innovative mushroom-based insulation material, Greensulate, which was developed by two industrious college students, for several years. The YouTube videos I watched about it were a lot of fun. Yeah, yeah, I thought. This would be a cool product if it ever gets to the stage of actual production--skeptical that that would occur. A lot of great ideas never get to the point of actual production.
But then a few weeks ago, I received a package from a friend who works for one of the nation's largest building products manufacturers. Included was a sample and a postcard-sized brochure about the material. "Have you heard of it," my friend asked me?
Actually holding a sample of a product--even if it still is a prototype--and reading through actual printed literature lends an air of reality to good ideas. I'm becoming a believer. What is Greensulate?
Greensulate is an R-3-per-inch rigid insulation material that is made from intertwining mycelium (rootlike filaments of a fungus) that are grown in agricultural waste materials (primarily seed hulls) under controlled conditions. The mycelium forms a foam-like material that insulates reasonably well.
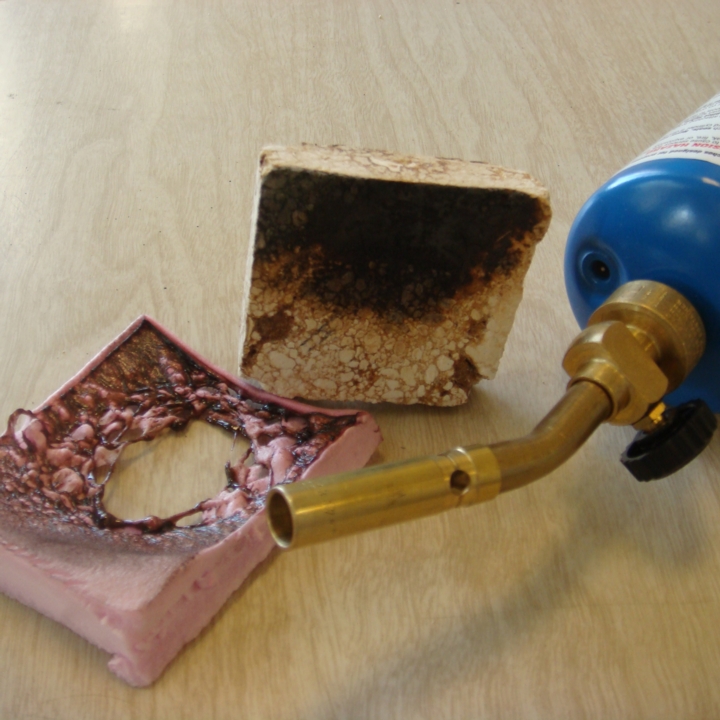
The sample I received looks a lot like the soy product tempeh, which you can find in health food stores. In fact, Greensulate is not all that different from tempeh, which is a fermented soy product made by inoculating soybeans with the fungus Rhizopus oligosporus. The fungus grows on the soybeans, converting the soy into a nutritious, fairly homogenous cake.
As I looked at the Greensulate sample, I was reminded of the various piles of wood chips I've had for our garden over the years--and how fungus sometimes creates clods that hold together. That's how inventors Eben Bayer and Gavin McIntyre first got the idea for Greensulate--while mechanical engineering undergraduates at Rensselaer Polytechnic Institute (RPI) in Troy, New York.
SUPPORT INDEPENDENT SUSTAINABILITY REPORTING
BuildingGreen relies on our premium members, not on advertisers. Help make our work possible.
See membership options »Bayer and McIntyre were in a class together at RPI, Inventor's Studio, and pursued how to use the mycelium that grew on wood chips as a resin--creating Greensulate. The two founded Ecovative Design after graduating in 2007 and succeeded in attracting some small start-up grants to produce samples and demonstrate commercial potential. These small grants were followed by larger grants from the New York State Energy Research and Development Authority (NYSERDA) and the U.S. Environmental Protection Agency (EPA) to further develop the ideas and build a 10,000 ft2 prototype manufacturing plant, which is now operating in Green Island, New York, near Albany.
In the manufacturing process, according to chief scientist Gavin McIntyre, a waste agricultural material, such as buckwheat hulls or rice hulls, is inoculated with the fungal spores and poured into molds. The molds are placed under carefully controlled conditions for five to ten days, during which time the fungal mycelium (root-like fibers) grow throughout the agrifiber matrix, literally growing the rigid foam. After removal from the forms, the Greensulate material is treated to stop the mycelium growth and sterilize the material. The company claims that in a wall system, the insulation will remain inert as long as it's kept from getting soaked. A number of different fungus species are being tested by the company, including one that produces a mold-resistant foam that meets the ASTM standard C-1338.
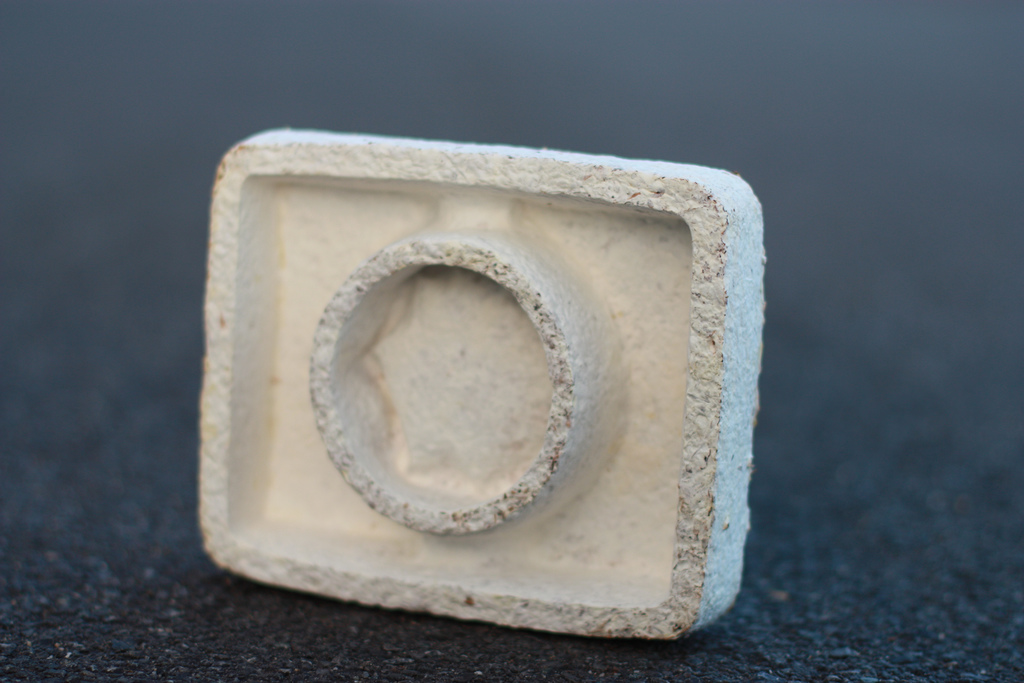
The finished Greensulate insulation contains no VOCs, no chemical flame retardants, no plastics or other artificial materials. It is all natural, and unlike some biobased materials, does not use a food product. While the product achieves R-3.0 per inch today, "we believe we can get the R-value higher, said McIntyre. While stable and inert in use, Greensulate breaks down fairly quickly in a compost bin.
Ecovative Design has some demonstration projects for building insulation as well as acoustic panels. "We're currently positioning that technology for structural insulating panels" (SIPs), McIntyre told me. In this application, the Greensulate cores are grown first, then sandwiched between oriented strandboard (OSB) skins and put in the glowing chambers for another 24 hours. The mycelium provide the binder to permanently bond the OSB skins to the core insulation--replacing polyurethane binders that are commonly used with expanded polystyrene (EPS)-core SIPs.
The company is six months into a 24-month Greensulate testing phase for the manufactured housing industry. If all goes well, the company should have SIPs on the market in 2012. A Class 1 fire rating has already been obtained, according to the company. Other properties include Compressive Modulus of 2100 psi (ASTM C165-07), Flexural Strength of 100 psi (ASTM C203-05) and Flextural Modulus (ASTM C203-05). The density is currently listed as 6-12 lbs/ft3.
While a building insulation is still a ways down-the-road, Ecovative Design is currently making a commercial packaging foam, EcoCradle, which is being used today by systems furniture manufacturer Steelcasefor protecting the company's "ready to assemble" furniture during shipping. The packaging foam is custom-made using forms that fit the application--such as corner protectors. At the end of its use, EcoCradle packaging can simply be thrown into a standard compost bin, and it will decompose. (Most other biobased "compostable" plastics will only decompose quickly when finely shredded in carefully controlled industrial composting facilities.)
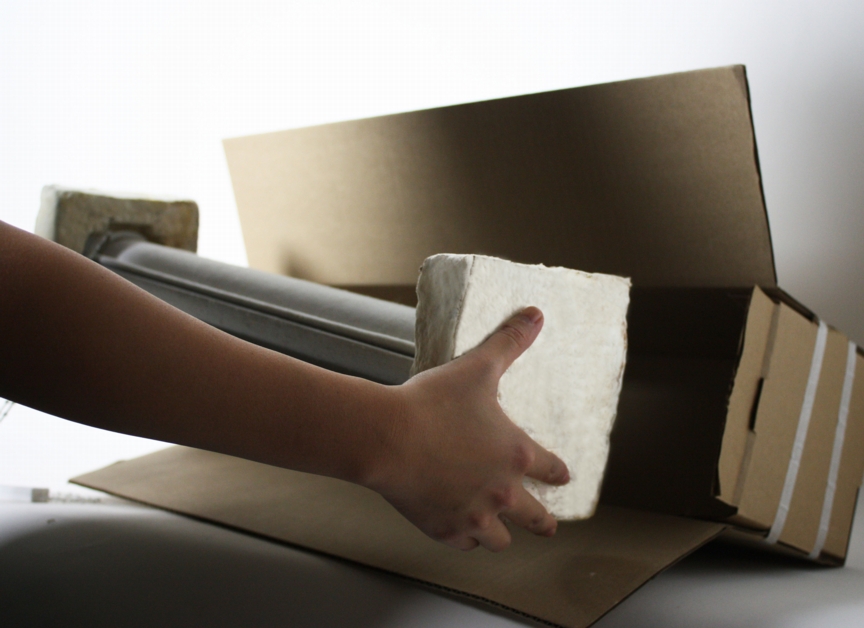
In addition to Steelcase, EcoCradle packaging foam is also being supplied to Bloomberg Financial, which uses it in shipping their custom keyboards. A contract with another large customer is nearing finalization, according to McIntyre. "We're getting tremendous response," he told me. "Our current constraint is capacity." The company is manufacturing packaging foam in its New York factory, but will be expanding shortly. Ecovative Design expects to double capacity during 2011 and open a West Coast plant in 2012, according to McIntyre.
Because the raw materials are inexpensive (waste agricultural fibers and fungal inoculant), Ecovative Design expects Greensulate insulation to be cost-competitive with foam insulation materials once manufacturing is scaled up; the goal is price parity with polystyrene, according to company CEO Eben Bayer.
For more information:
Ecovative Design, LLC
Green Island, Ney York
518-273-3753
Alex Wilson is the executive editor of Environmental Building News and founder of BuildingGreen, Inc. In addition to this product-of-the week blog, he writes the weekly Energy Solutions blog. To keep up with his latest articles and musings, you can sign up for his Twitter feeds. Products covered in his product-of-the-week column are--or soon will be--listed in BuildingGreen's GreenSpec Directory.
Published January 6, 2011 Permalink Citation
(2011, January 6). Greensulate – A fungus-based insulation material that's grown rather than manufactured. Retrieved from https://www.buildinggreen.com/blog/greensulate---fungus-based-insulation-material-thats-grown-rather-manufactured
Comments
Contacts in Australia
Hi, Tony!
We have covered hemp products in the past: https://www.buildinggreen.com/primer/hemp-durable-low-carbon-building-ma...
It doesn't dive deep on insulation, but R-3.5 is correct.
HEMP
Can you please write a post on HEMP/HempWool, Hemcrete etc... Besides the taboo and the insane laws and regulations, the material supposedly have an r value perhaps at 3.5 per inch? it has been used for centuries, and if true, then it should gain more focus.
Insulation for timber framed house
I wish to build my own timber framed house useing Mycelium insulation panels ,where in UK
Can I buy ?
Mycelium insulation for walls
i have a tiny cabin, off-grid in Joshua Tree, CA. I want to insulate it with greensulate/mycelium insulation. Where can I buy it in or near California? Do rodents like to eat it/burrow in it like the fiberglass insulation? Will it withstand desert heat - up to 120degrees? Thank you
Add new comment
To post a comment, you need to register for a BuildingGreen Basic membership (free) or login to your existing profile.